Thank you for following this blog series on how preconstruction strategies can prevent delays and change orders. In the first post of this series I outlined an outcome-based approach to documenting the owner’s project requirements and design intent along with tips to integrate that rigor through the design development, permitting and pricing documents. Today’s post is about how to avoid the dreaded RFI (“Request for Information”).
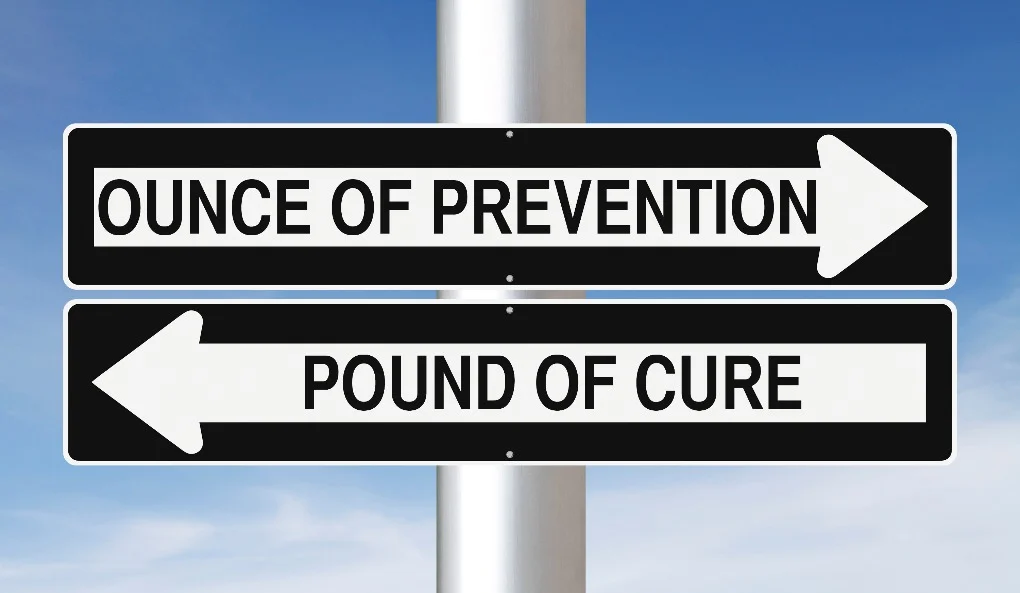
At the end of the day we only have so much bandwidth at any given time. The time we spend clarifying the scope to make it “buildable” takes away from the time we need to plan and sequence material deliveries, equipment and workers. Increasingly, the design quality assurance process is delegated to the contractors in hopes this strategy will reduce the amount of documents (and design costs) required. However, in practices, this strategy results in avoidable change costs and delays while still incurring the design costs – just pushing design costs into the construction administration phase. This post provides a basic framework to discover errors and omissions during the design phase.
RFI “proofing” starts with a strategy and ends with a procedure. The strategy catches the foundational issues that, if in error, require redesign. Once the foundational integrity is confirmed, the final step is to use a procedure to make sure the intent is complete and constructable. The result is a set of documents that attracts reliable and complete pricing with much less administrative burden on the contractors, design team and owner.
We start with the strategy because If elevations or dimensions are in error, everything connected to those elements could also be affected by the necessary adjustments, a procedural scrub might be rendered obsolete by the design revisions forthcoming. For example, during the design phase there are options to raise or lower the slab and adjust other grades and structures to mitigate design errors. Later in construction many of these variables will be set and options to mitigate are few, time consuming and expensive.
The Strategy: Each project has different components but the following list should be generally applicable to any commercial structure and building type. Review the entire list of required corrections before making any adjustments to avoid iterations.
Suggested order of QA:
-
Accessible path. Do grades and elevations meet code from entries and parking areas to the public right of way connection? If not, should the slab be raised or lowered?
-
Utility access and connections. Where are storm water, sanitary sewer, high voltage, natural gas and domestic / fire water taps at the right-of-way? Are the size and elevation of these connections consistent with the equipment room locations and requirements?
-
Load bearing path and shear. Which walls support the roof? Do these load paths flow directly to the foundation. Which walls are shear walls and which side does the shear reinforcement occur? Do they align? Does their location conflict with acoustical mitigation or openings?
-
Roof drainage plane(s) and drains through building. Does each roof surface slope to drain(s)? Is there adequate room for drain assemblies in ceiling space? Are you able to follow these drain stacks down through and out of the building to the connection in the site / public right of way?
-
Elevator pit, shaft, penthouse. Is the shaft and pit clear of all other structural elements? Does the top of the shaft fit below the maximum building height? Is there adequate space and adjacency for elevator equipment and electrical gear?
-
Vertical shafts and horizontal utilities distribution. Are shafts stacked vertically with clear dimensions from 1st floor to roof? Are floor and shaft penetrations clear of structural reinforcement? Does clear space above ceiling and structural beams / posts accommodate horizontal duct, fire sprinkler and plumbing supply / recirculation routes? Are electrical and low voltage sleeves stacked vertically or routed through shafts?
-
Fire rating strategy, exit path. What is the strategy to contain smoke and fire ratings? Are all penetrations and access noted for ratings and practical to achieve?
-
Window and door locations, sizes. Are there any conflicts with structure or privacy? Are there routes below or above openings for electrical, condensate drains, etc? Are all ADA clearances accommodated? Is tempered or fire rated glass required?
-
Plumbing and casework ADA compliance. Confirm that fixtures and elevations indicate dimensions they must conform to. Most ADA dimensions have a tolerance range or maximum. Consider using dimensions that allow for variations on site without coming out of compliance.
-
Local ventilation, drainage and utility connections. Do equipment rooms and doors provide adequate room for equipment placement, and required clearances? Are doors large enough to get equipment in and out? Are vents, drains and connections noted and available?
-
Schedules and calculations. Double check to make sure that room numbers, area calculations and building dimensions are accurately noted and correct. These basic dimensions if in error can create substantial revisions if found during construction.
-
Building Envelope. Are there sections provided at each side of every exterior opening? Are sections provided for each transition from one material to the next? Are control joints detailed and coordinated with window and door locations?
The Procedure. After the strategy tasks are competed and confirmed to be in alignment with the design intent, perform the following strategy for each page of the plans:
Start by tying every keynote on each plan to the locations they occur on the drawing and follow every detail flag to catch any errors or omissions in documentation. Then drill down using the list below:
-
Does the note clearly describe the requirement? Is more information available in the specifications or other drawings, details?
-
Do general notes refer to other requirements for submittals and approvals from the city or utility providers?
-
Does the location require / provide a reference to a detail?
-
If so, is the detail included where noted and in sufficient detail to order materials?
-
Are clearance and connection dimensions included to layout and assemble the work?
-
Is an equipment or performance specification necessary to install or connect equipment provided by others? If so, where will the underlying specification be made available to contractors? Is contact information provided for questions?
-
If submittals are required, is the scope of the submittals clear and appropriate?
-
Are mockups required? What is the scope of the mockup? Is it appropriate and complete (not just boilerplate)?
Ok, perhaps RFI “proof” may not be attainable. No matter how rigorous the planning, there will be concealed conditions, dimensional errors, supply chain driven substitutions and permit comments to accommodate. But why stack those unavoidable tasks on top of those we can discover and correct in the design phase? An effective strategy and procedure will result in more accurate and enforceable pricing, fewer delays, lower construction administration costs and a much more enjoyable construction project and I will argue – at a much lower dollar (and human) cost than trying to solve these issues during construction.
I hope you enjoyed todays post and if so, please follow, comment, share and like as we walk through more best practices to use preconstruction practices to improve construction outcomes. If you want to see how these practices can work on your project – let’s talk!
Thanks…Chris